Our Mission
We partner with our customers, colleagues, & suppliers to help them innovate and discover new possibilities.
We engineer, manufacture, and deliver solutions for the equipment that powers our lives. From compressors to turbines, vacuum pumps to reciprocating engines, Solberg’s products can protect equipment and work environments in the most challenging applications.
For more than 50 years, we have embraced the ideal of industrial growth while advocating for environmental responsibility and safe working spaces. We always strive to stick to our guiding principles:
Succeed as a family
Do the right thing
Endeavor to be the best
Take care of the customer
Love the planet
Play hard to win
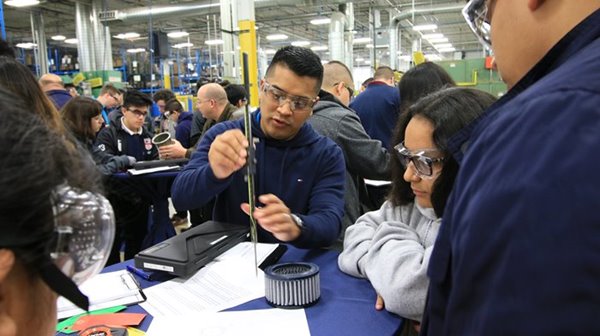
An Imagination for Innovation
We believe that curiosity, imagination and an appetite for learning are crucial parts of solving our customers’ industrial filtration challenges. At Solberg, we never stop looking for ways to improve our filtration, separation, and silencing products. We want to create smart new solutions that meet market needs.
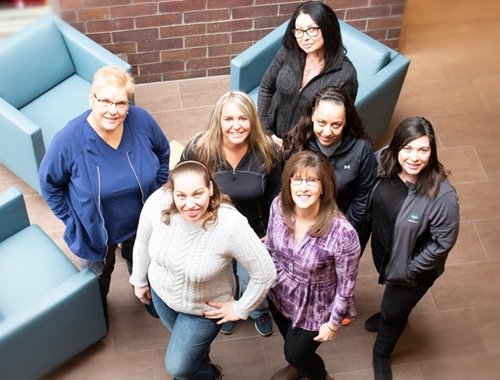
A Dedication to Partnership
We’re more than a source for quality filtration, silencing and separation products. We act as a true partner to all of our customers. We approach each challenge with enthusiasm, creativity and expertise, and pride ourselves on finding tailored solutions for unique situations.
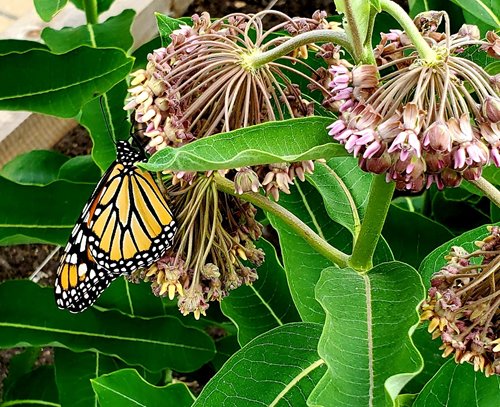
A Commitment to the Environment
At Solberg, we embrace innovation while still advocating for environmental responsibility. We focus heavily on the development of sustainable solutions that protect mission-critical machinery and the surrounding environment. Read more about our commitment to sustainability here.